Are You Using The Best Ultrasonic Cleaner Solution? Here’s How to Know Which Detergent To Use
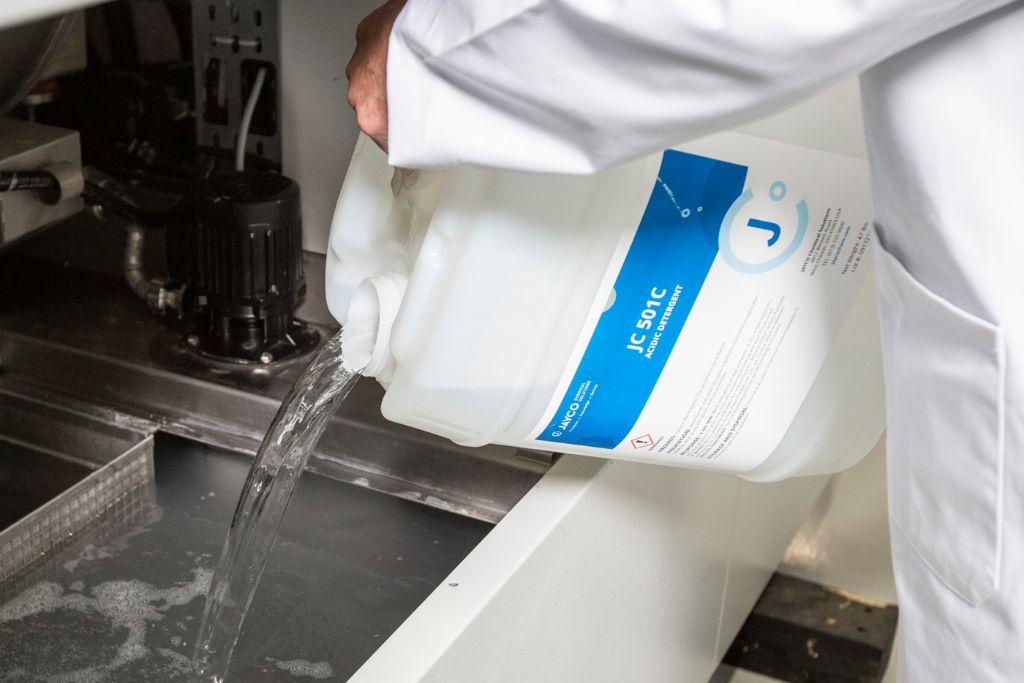
Ultrasonic cleaning has become an essential part of many industries, from automotive to medical. By using sound waves to create cavitation bubbles, ultrasonic cleaners can remove contaminants from intricate and hard-to-reach areas, providing a deep clean that’s difficult to achieve with other methods.
However, the effectiveness of an cleaning process doesn’t just depend on the machine—the cleaning solution you choose is equally important. Selecting the best ultrasonic cleaning solution for your specific application can make the difference between a spotless result and a lackluster outcome.
In this guide, we’ll walk you through how to choose the right ultrasonic cleaner solution to ensure maximum cleaning effectiveness.
How Ultrasonic Cleaners and Ultrasonic Cleaning Systems Work
Ultrasonic cleaners work by producing high-frequency sound waves in a cleaning bath, creating tiny cavitation bubbles that collapse and dislodge contaminants from surfaces. This cavitation process is the key to achieving a thorough clean, but it needs the right cleaning solution to be truly effective. The cleaning solution aids in breaking down oils, rust, or other contaminants, enhancing the cavitation effect and ensuring that the surfaces are thoroughly cleaned.
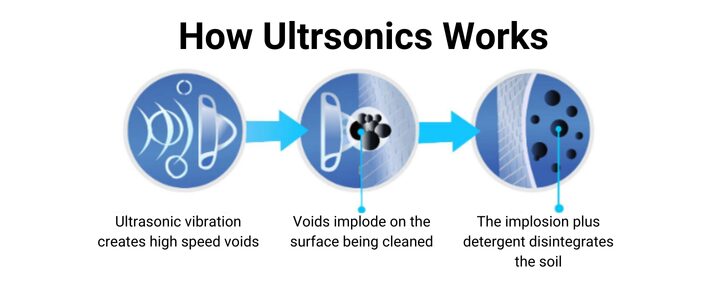
Factors to Consider When Choosing the Correct Ultrasonic Cleaner Solution
1. Type of Material Being Cleaned
Different materials require different cleaning solutions to avoid damage while ensuring cleanliness. For example:
- Metals: Stainless steel, aluminum, and brass each have unique requirements. Stainless steel can withstand a wide range of solutions, while aluminum requires a more delicate approach to avoid etching or surface finish issues.
- Non-metals: Plastics, glass, and ceramics are sensitive to certain chemicals, so selecting a compatible solution is crucial.
2. Type of Contaminant
Identifying the contaminant is key to choosing the right solution:
- Oil and Grease: Common in automotive and industrial applications; degreasers or alkaline solutions are usually effective.
- Rust and Scale: Acidic solutions are often used to remove rust, though they must be selected with care to prevent damage to the part.
- Organic Residues: Dirt, dust, and biofilms require tailored solutions, often special alkaline solutions or enzymatic for biological contaminants.
3. Level of Cleaning Required
The cleaning solution should be matched to the level of cleaning needed:
- Light Cleaning: Routine maintenance cleaning may only require a gentle detergent.
- Cleaning of Manufactured Parts: A neutral or alkaline solution often works best for most materials.
- Deep Cleaning and Restoration: Heavily soiled items might need stronger acidic solutions or solvents.
- Rebuild Operations: Carbon or heavily dried on soils usually require highly alkaline solutions.
- Critical Cleaning To Industry Specifications: For industries such as aerospace, medical, and optical, solutions must meet stringent cleanliness certifications to ensure product quality and compliance with industry standards.
4. Cycle Time
Some solutions can reduce cycle times by cavitating better or being more aggressive, while others may require longer cycles for thorough cleaning. Finding a balance between cleaning speed and thoroughness is important for efficiency.
5. Bath Life Maintenance
The longevity of the cleaning solution is another factor. Some solutions can be used for months before needing replacement, while others require fresh solution in the cleaning tank to maintain effectiveness. High quality solutions allow for monitoring and adding additional detergent to maintain optimal ultrasonic cleaning process performance.
6. Rinsability
The ease with which a solution can be rinsed off matters, especially for applications requiring a spotless finish or parts that will have a coating applied. Residue left behind can be problematic, so choosing a solution that rinses cleanly is essential.
7. Detergent Cost per Part Cleaned
Cost-effectiveness is a consideration for high-volume operations. The solution should provide the desired cleaning quality while being affordable for routine use. It’s not just the cost per gallon but the cost per correct ultrasonic cleaning solution required in the bath to clean sufficiently.
Types of Ultrasonic Cleaner Solutions for Best Results
1. Water-Based Solutions
These are often eco-friendly and safe for a wide range of applications. They are suitable for light to moderate cleaning but may not be effective on heavy contaminants.
2. Solvent-Based Solutions
Solvent solutions can be highly effective but often come with safety and environmental concerns. They are best suited for stubborn contaminants like grease but require proper ventilation and disposal.
3. Enzymatic Solutions
Enzymatic cleaners are ideal for medical, dental, and biological applications where organic residue removal is crucial.
4. Acidic vs. Alkaline Aqueous Solutions
- Acidic Solutions: Effective for removing rust and scale but can be harsh on some materials.
- Alkaline Solutions: Great for degreasing and general cleaning, offering versatility for many applications.
pH Level | Best Used For | Compatible Materials |
---|---|---|
Acidic (pH < 7) | Rust and scale removal | Stainless steel, iron |
Neutral (pH ~ 7) | Light to moderate cleaning | Most materials |
Alkaline (pH 8 -11) | Degreasing and general cleaning | Most metals including cast iron, steel, stainless steel, aluminum, zinc, copper, brass. Glass, ceramics and plastics are typically safe as well. |
Highly Caustic (pH > 12) | Heavy-duty oil and wax degreasing. Removal of stubborn contaminants such as carbon and polishing compounds. | Stainless steel, heavy-duty metals |
Different Types of Ultrasonic Parts Washers and Ultrasonic Cleaning Equipment
1. Tabletop Immersion Ultrasonic Cleaners
Tabletop ultrasonic cleaners are compact and ideal for smaller parts or low-volume cleaning tasks. They are suitable for applications in laboratories, dental clinics, and small workshops. Their portability and ease of use make them a popular choice for those needing quick, effective cleaning on a smaller scale.
2. Large Industrial Ultrasonic Tanks
These are heavy-duty ultrasonic cleaners designed for large or complex parts that require thorough cleaning. Large industrial ultrasonic tanks are commonly used in industries such as automotive, aerospace, and heavy manufacturing. They offer the ability to clean multiple parts simultaneously and are perfect for high-volume operations.
3. Rotary Basket Washers
Rotary basket washers combine ultrasonic cleaning with spray and rotation, ensuring that all surfaces of the part are exposed to the cleaning solution. This type of washer is ideal for intricate parts with blind holes or complex geometries, as the rotating action helps to dislodge contaminants from hard-to-reach areas.
A special formulation that both cavitates well while not foaming is the best solution, which many typical alkaline cleaning solutions don’t do well. See the Jayco line of Hybrid Clean products for vacuum assisted rotary basket washers like MAFACs.
Why General Purpose Ultrasonic Detergents Might Not Be the Best Choice
While general-purpose detergents may seem like a convenient option for ultrasonic cleaning, they often fall short in delivering optimal results. Here are some reasons why specialized ultrasonic cleaning solutions are usually a better choice:
- Ability to Cavitate: General-purpose detergents may not be formulated to enhance the cavitation process effectively. Without proper cavitation, the cleaning power of the ultrasonic cleaner is significantly reduced, leading to subpar results.
- Rinsability: General-purpose detergents often leave residues that are difficult to rinse off. This can be problematic for applications requiring a spotless finish, as leftover residue may affect the performance or coating adhesion of the cleaned part.
- Ability to Maintain Tank Life: Specialized ultrasonic cleaning solutions are designed to maintain their effectiveness for multiple cycles, whereas general-purpose detergents may break down more quickly. This means that general-purpose detergents often need to be replaced more frequently, leading to increased maintenance and downtime.
- Concentration Required: General-purpose detergents typically require much higher concentrations to achieve acceptable cleaning results. This not only increases the cost per part cleaned but also makes it more difficult to manage solution consistency, ultimately reducing efficiency.
Precision Ultrasonic Cleaning for Critical Industries
Precision cleaning is crucial in industries where even the smallest contaminants can affect product quality, performance, or safety. Aerospace, medical, and optical industries require ultrasonic cleaning solutions that are specifically formulated to meet stringent cleanliness certifications and standards.
- Aerospace: In aerospace applications, parts must be free from any contaminants that could compromise safety or functionality. Aerospace ultrasonic cleaning solutions are formulated to remove oils, carbon residues, and other contaminants while meeting strict regulatory standards of the OEM manufacturers. Cleaning is also critical to removal of dyes from FPI stress fracture detection. Examples of Jayco aerospace ultrasonic cleaners are JC 300C and JC 301SC.
- Medical: Medical devices require an exceptionally high level of cleanliness, especially when used in life-critical applications. Medical detergents must promote cavitation for effective removal of particulate and organic residues, both water based and oil based. Rinsing is also important as medical devices require a residue free surface. Endotoxins and bioburden are critical tests these specialized cleaners must pass. Ultrasonic cleaners used in the medical device manufacturing often utilize specialized solutions that are effective in removing manufacturing residues while being biocompatible and meeting ISO 13485 along with other medical standards. In hospital operations an enzymatic solution may be used to remove organic material from surgical procedures. Examples of Jayco medical device ultrasonic cleaners are JC 400M and JC 401M.
- Optical: Optical components, such as lenses and mirrors, require spotless cleaning to ensure clarity and performance. Optical ultrasonic solutions are formulated to remove dust, fingerprints, and polishing compounds like cerium oxide prior to coating applications and must rinse thoroughly without leaving any streaks or damaging delicate surfaces. Examples of optical ultrasonic cleaners are JC-Optic 400 and JC-Optic 700.
These industries cannot compromise on cleanliness, and using the right ultrasonic cleaning solution is key to achieving the required level of precision and compliance with industry standards.
Safety and Environmental Considerations for Ultrasonic Cleaning Solutions
When selecting an ultrasonic cleaner solution, safety should be a top priority. Many solutions contain chemicals that require careful handling, appropriate storage, and proper disposal. Consider opting for eco-friendly solutions when possible to minimize environmental impact, and always follow manufacturer guidelines to ensure safe usage.
Summary
Choosing the right ultrasonic cleaner solution is essential for achieving optimal cleaning performance, ensuring safety, and maintaining cost-effectiveness. By understanding the materials, contaminants, and specific requirements of your application, you can select a solution that enhances the cavitation process, extends bath life, and meets industry standards. Whether you’re working in aerospace, medical, or industrial settings, the right detergent can elevate your cleaning process from adequate to exceptional.
For more information on tailored ultrasonic solutions, explore the full range of products from Jayco Ultrasonic Cleaners and discover how the perfect cleaning solution can transform your workflow.