Ensuring Aerospace-Grade Cleanliness: The Power of Properly Engineered Spray Wash Detergents for Parts Washers
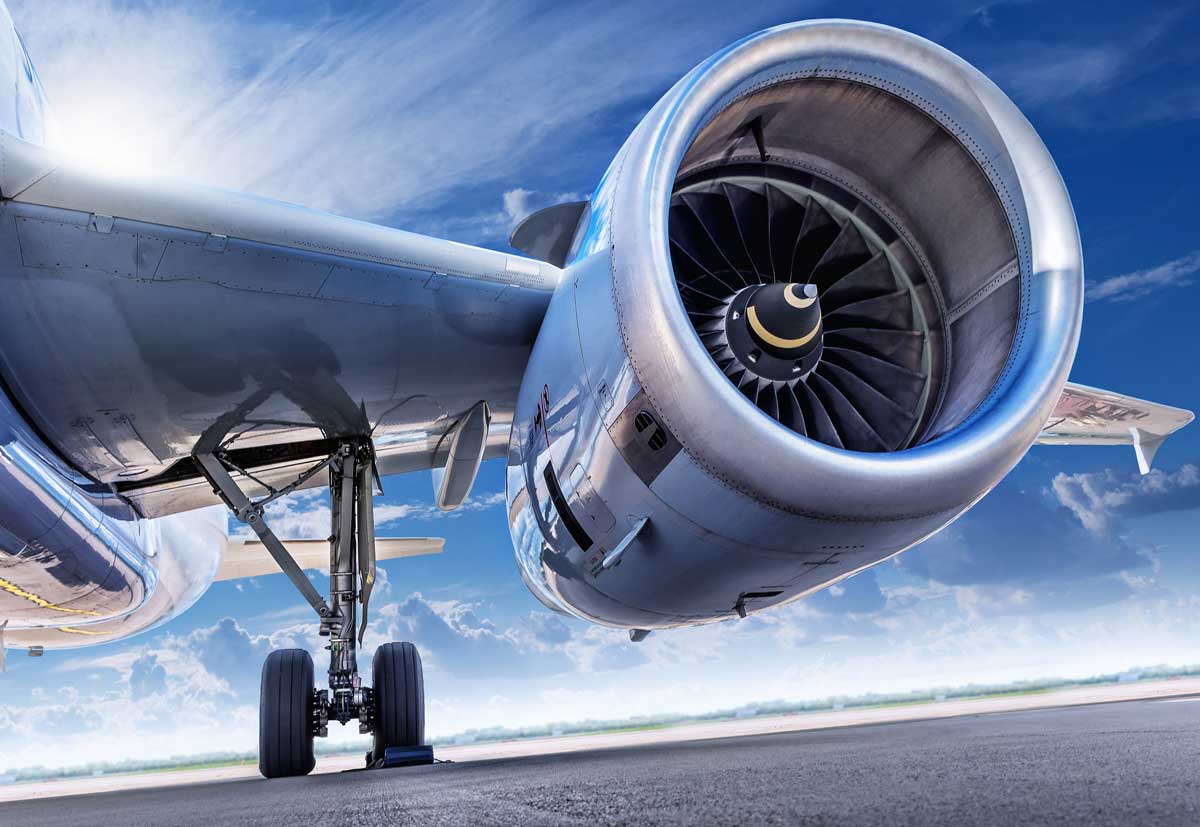
In the aerospace industry, meeting stringent cleanliness standards is crucial for ensuring component reliability and performance. A well-formulated aqueous alkaline spray wash chemistry is essential for effectively removing tough contaminants such as grease, oils, BOE lube, Krytox, and fluorescent penetrant inspection (FPI) residues.
If not properly removed, these residues can compromise the structural integrity, surface finish, and functionality of aerospace components. Cleanliness is particularly critical before processes like heat treatment, plating, anodizing, non-destructive testing, and packaging, as any residual contamination can negatively impact the final part quality.
Common Challenges in Aerospace Parts Cleaning
Material Compatibility
Aerospace components are made from diverse materials, including aluminum, steel, titanium, nickel alloys, and composites. Cleaning chemistries must be compatible across these substrates to prevent corrosion, etching, or degradation.
Standards such as ASTM F945, F519, F483, and F1110 guide the evaluation of stress corrosion, hydrogen embrittlement, and immersion/sandwich corrosion risks to ensure the safety and longevity of components.
JC 301SC, for example, is a low-foam alkaline detergent designed for spray wash systems. Its formulation ensures compatibility with metals like titanium, stainless steel, and aluminum while maintaining compliance with ARP 1755B and ASTM standards
Soil Removal
Effective cleaning chemistry must tackle a wide array of soils. BOE lube, Krytox, and FPI residues pose a significant challenge due to their extreme adhesion and resistance to removal.
Aqueous alkaline chemistries remove these soils by breaking them down through saponification, emulsification, and dispersion. This process ensures that no residual contamination remains, preventing interference with surface coatings, bonding, or overall performance.
New Part Prove Out
Cleaning processes are often designed for an existing group of parts that have been manufactured or processed over an extended period. However, introducing a new part into the process can present significant cleaning challenges.
Incomplete cleaning may result from a different oil required for the new machining or forming process. Additionally, new parts often feature tighter tolerances, blind holes, or intricate channels, all of which can make proper cleaning more difficult.
The Importance of Non-Foaming Detergent in Spray Wash Systems
Spray wash systems, including inline, spray cabinet, and Vacuum Assist Clean and Dry (VACD) technologies, rely on high flow and consistent pressure for optimal cleaning performance.
Today it is common for a heavy dose of defoamer to be used in an attempt to control the foam. This is a band-aid on a broken leg.
Often the foaming issue has been a part of the wash process for so long that it gets ignored and becomes accepted. Excessive foaming can disrupt operations and slow cycle times thru:
- Foam fouls level sensors interfering with proper solution level
- Obstructing spray nozzles and reducing flow rates
- Impairing visibility and process monitoring in enclosed systems
- Introducing inefficiencies in rinse stages and water reclamation processes
Low-foaming chemistries like JC 301SC are engineered to mitigate these risks, ensuring operational efficiency and consistent cleaning results. Such formulations are critical for spray systems operating at elevated temperatures (140°F-170°F), as foam generation often increases with decreasing temperature unless specifically controlled.
Common Questions from Aerospace Manufacturers
What are basic safety tips for aerospace cleaning?
While it might seem redundant, our experience shows that basic safety precautions are sometimes overlooked. To protect workers, ensure the use of protective glasses, aprons, gloves, and provide adequate ventilation in work areas. Additionally, ear protection is important due to the noise levels in shops.
Education is essential. Workers should understand the nature of the chemicals they’re handling. Review safety policies regularly, particularly after process changes. As cleaning processes evolve, so should your safety measures.
What are the best oil removal methods?
Cleaning chemistries have a soil “capacity,” and once exceeded, soils can redeposit onto parts. The choice of method depends on the type of oil:
- Water-soluble oils are challenging as they dissolve into the cleaning solution. Indicators like foaming or water spots suggest high oil loading. Frequent monitoring and proactive dumping of the wash tank are critical.
- Non-soluble oils are easier to remove because they separate and float. Skimmers can be effective but are often oil-specific. Coalescing oil systems are more versatile and efficient, allowing for greater chemistry capacity and better oil removal through overflow or gravity-based systems. Cleaning chemistries designed to split oils enhance these systems’ performance.
Why are my parts still dirty?
Achieving consistent cleanliness requires monitoring beyond adding detergent. Use titration kits to check concentrations and monitor process parameters like rinse water quality. Conductivity meters are invaluable for maintaining rinse water quality. Rising conductivity indicates contamination and necessitates action, such as increasing water flow or dumping the rinse tank.
How do I determine part cleanliness?
Part cleanliness is usually defined by customer specifications. For instance, Boeing’s BAC 5749 Alkaline Cleaning spec relies on the ASTM F22 Water Break Test to assess hydrophobic surface films. Alternatives include dyne solution or test inks to evaluate surface energy.
Quantitative methods include:
- Nonvolatile residue (NVR): Measures residual material left after solvent evaporation.
- Particle count: Extracts and measures contaminants from a known surface area, comparing size and quantity against specifications.
Why Cleanliness Matters
Failing to remove contaminants like grease, Krytox, and FPI solution can have serious consequences including:
- Adhesion Failure: Residual oils or FPI dyes on surfaces can prevent proper bonding in adhesive joints or coatings.
- Corrosion Initiation: Trapped soils can create localized corrosion cells, compromising component durability.
- Performance Degradation: Contaminants left on precision components (e.g., bearings, actuators) can lead to increased friction, wear, or outright failure during operation.
In conclusion, a well-formulated aqueous alkaline spray wash chemistry, coupled with strict adherence to aerospace cleaning standards and continuous monitoring of process variables, ensures effective removal of tough contaminants while maintaining material integrity. Non-foaming solutions specifically designed for modern spray wash systems are essential for meeting the rigorous cleanliness requirements of the aerospace industry.