Aerospace and Aviation Cleaner Solutions: Precision Parts Washer Chemistry for Aircraft
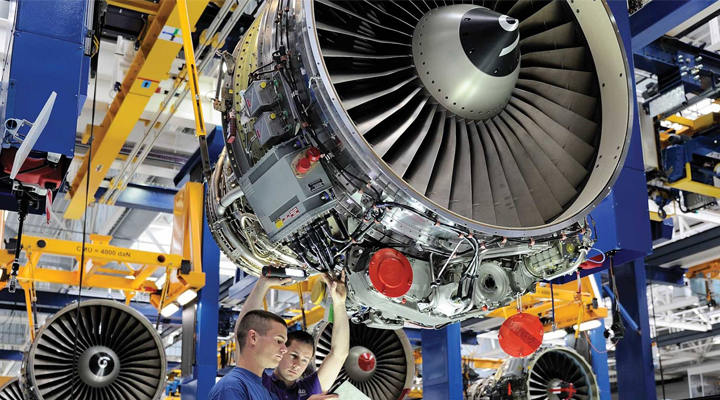
Maintaining cleanliness in aerospace and aviation parts is crucial for safety, performance, and regulatory compliance. This article provides an in-depth look at effective cleaning methods, from ultrasonic cleaners to spray washers, ensuring your aircraft components meet the highest standards. Learn how proper cleaning can optimize aircraft reliability and precision while exploring JAYCO’s aerospace-approved solutions that make the difference.
Importance of Proper Cleaning in Aerospace and Aviation
The aviation industry demands precision, and maintaining cleanliness in components is paramount. Contaminants such as dirt, grease, and carbon deposits can negatively impact aircraft performance, potentially causing malfunctions or accelerated wear on critical systems. To ensure safe and reliable operations, strict adherence to industry standards and regulations for component cleanliness is required. Proper cleaning mitigates these risks, helps components function as intended, and ensures compliance with aviation safety protocols.
Common Contaminants in Aerospace Parts Cleaning
Aerospace parts are exposed to various contaminants during both manufacturing and operational phases. These contaminants include:
- General dirt and grease: Accumulated during handling and operation.
- Dried de-icing fluids: Residues left from anti-icing procedures.
- Carbon dust: A byproduct from engine and exhaust systems.
- Machining oils: Used during manufacturing processes.
- Fluorinated greases: Specialty greases used in aviation components.
- Skydrol: A hydraulic fluid commonly found in aviation systems.
- Cosmoline: A corrosion-preventive compound used during storage.
These contaminants can be particularly challenging to remove, especially from complex parts with intricate geometries, requiring specialized cleaning methods to ensure the components meet performance and safety standards.
OEM vs. MRO Aerospace Parts Cleaning: Key Differences
OEM (Original Equipment Manufacturer) Parts Cleaning
OEM parts cleaning focuses on newly manufactured components, ensuring that all residues from machining and production processes are effectively removed. This type of cleaning is crucial for maintaining precision and meeting manufacturing standards. Common contaminants include machining oils, coolants, and residues from production.
MRO (Maintenance, Repair, and Overhaul) Aircraft Maintenance Cleaning
MRO cleaning involves servicing parts that have already been in operation. These components are often exposed to a broader range of contaminants, including carbon buildup, hydraulic fluids, and environmental debris. Cleaning agents used in MRO cleaning must be compatible with repair processes and non-destructive testing (NDT) methods to avoid compromising the integrity of parts undergoing inspection. The goal is to restore functionality while adhering to FAA or EASA maintenance standards.
Overview of Aerospace Cleaners and Surface Cleaning Methods
Manual Cleaning
Manual cleaning provides direct control over the process and is suitable for small or delicate parts. While effective for initial spot cleaning or precision tasks, it can be labor-intensive and may produce inconsistent results depending on the operator’s skill.
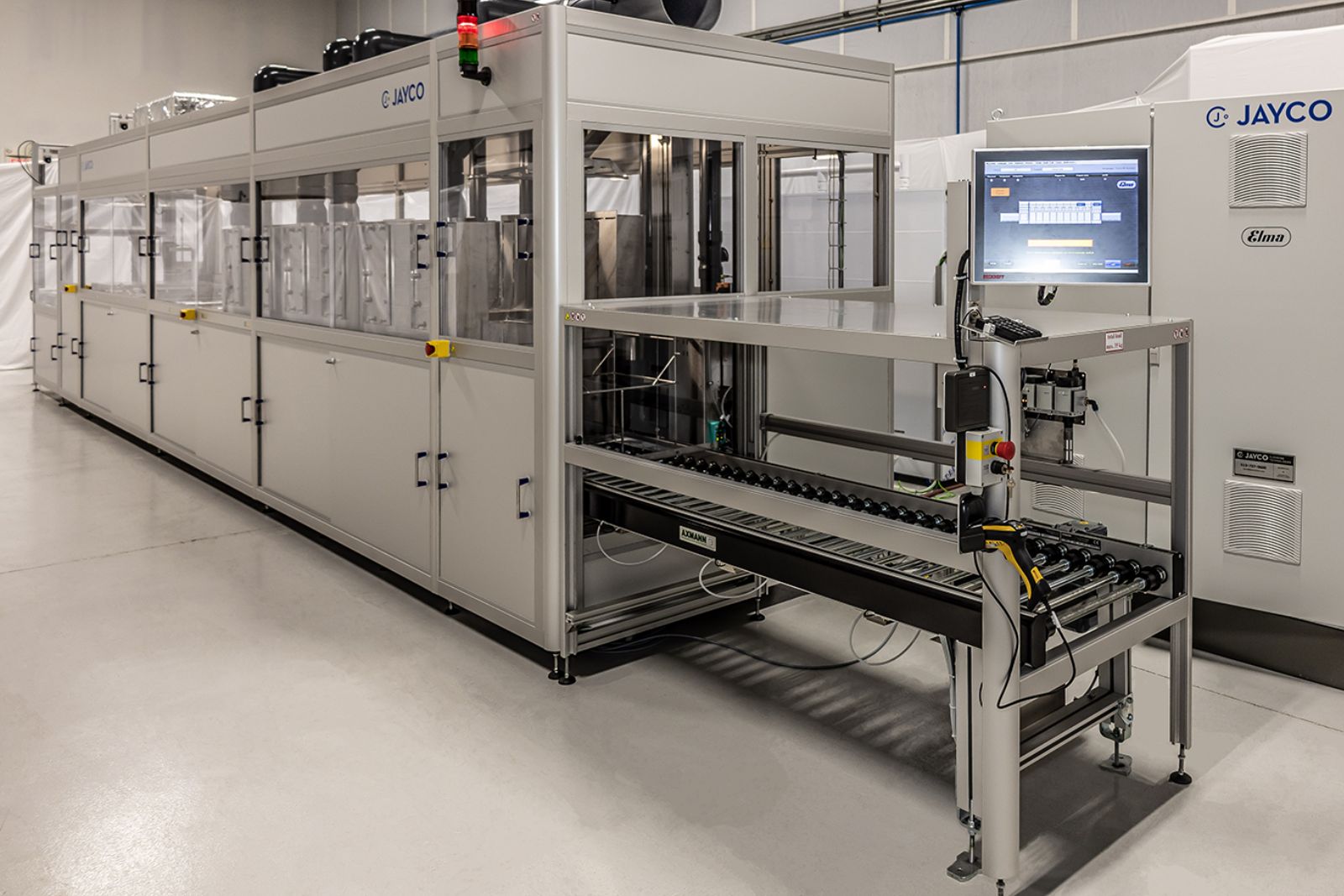
Ultrasonic Cleaning
Ultrasonic cleaning uses high-frequency sound waves to create cavitation bubbles in a cleaning solution, effectively removing contaminants from surfaces, including hard-to-reach areas. This method is ideal for intricate geometries and small components like bearings and valves. Ultrasonic cleaning is non-abrasive and highly effective for both OEM and MRO applications.
Featured Chemistry | JC 300C: Versatile, low-foam, alkaline detergent designed for use in ultrasonic cleaning applications. It effectively removes machining oils, light greases, and other production residues, and is suitable for use on various aerospace materials, ensuring compliance with industry cleanliness standards.
Spray Washing
Spray washing uses pressurized sprays of cleaning solutions to dislodge contaminants. It is highly efficient for cleaning large parts with simpler geometries, such as panels or casings. This method is advantageous for bulk cleaning and can significantly reduce cleaning times for large components.
Featured Chemistry | JC 701SC: Heavy duty high alkaline detergent for low foam applications. Removes machining oils, stamping lubes, grinding fluids, polishing/lapping compounds, and carbonaceous soils. Safe on steel, stainless steel, nickel alloys, vacuum melt alloys and titanium. RoHS, Reach and aerospace compliant.
Immersion Cleaning
In immersion cleaning, parts are submerged in a cleaning solution for extended periods to loosen and remove contaminants. This method is particularly effective for parts with complex geometries or heavy contamination, ensuring uniform cleaning across all surfaces. For immersion cleaning,
Featured Chemistry | JC 300C: Versatile, low-foam, alkaline detergent designed for use in ultrasonic cleaning applications. It effectively removes machining oils, light greases, and other production residues, and is suitable for use on various aerospace materials, ensuring compliance with industry cleanliness standards.
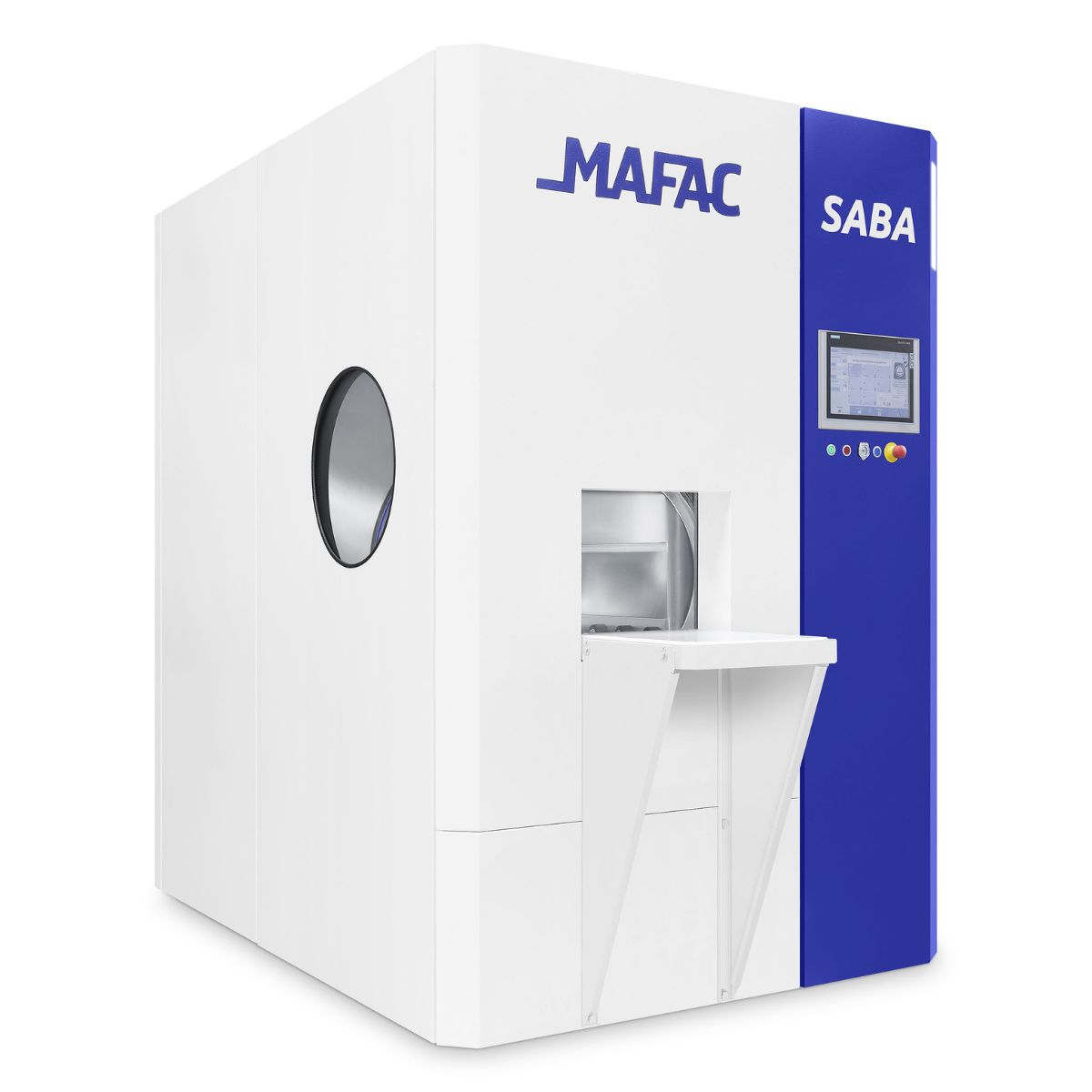
Rotary Basket Washers
Rotary basket washers use rotating baskets to provide thorough cleaning of parts. This method combines mechanical action with cleaning solutions to effectively remove contaminants from complex parts. The rotation ensures that all surfaces are exposed to the cleaning solution, making it ideal for components with intricate geometries or blind holes. Rotary basket washers are commonly used for parts with moderate to heavy contamination and are effective for both OEM and MRO applications.
Featured Chemistry | JC 301SC: Low foam heavy duty alkaline detergent, safe on titanium, ferrous and non-ferrous metals including aluminum. Used for removal of machining oils, stamping oils, and grinding compounds. Aerospace approved.
Cleanliness Testing for Aerospace and Aviation Parts
Determining Part Cleanliness
The cleanliness of aerospace and aviation parts is typically determined by the customer’s requirements or specific written standards. To meet these standards, it is essential to use consistent and valid testing methods.
Common Cleanliness Tests
- Water Break Test: Used to determine hydrophobic surface films, as specified by Boeing BAC 5749 and ASTM F22 standards.
- Dyne Solution or Test Ink: Evaluates surface energy by observing the behavior of ink on a surface.
- Nonvolatile Residue (NVR): Measures residual materials left after evaporation of a solvent.
- Particle Count: Extracts and measures particles from a known surface area, comparing them to allowable specifications.
Combining multiple tests may be necessary for complex surfaces or particularly demanding applications to ensure compliance with cleanliness specifications.
Key Certifications, SDS, and Approvals for Aerospace Cleaning Chemistries
Corrosion and Material Compatibility Tests
- ASTM F483: Total immersion corrosion testing.
- ASTM F519: Hydrogen embrittlement testing for high-strength steels.
- ASTM F1110: Sandwich corrosion testing for layered materials.
- ARP 1755B: Stock loss testing for material loss.
- ASTM G2111: Intergranular attack inspection.
- ASTM F945: Titanium stress corrosion testing.
Industry Standards and Certifications
Aerospace cleaning agents must comply with industry standards such as SAE AMS and ISO standards for quality management and environmental compliance. OEM-specific approvals from companies like Boeing and Airbus, as well as environmental and safety certifications like EPA, REACH, and RoHS, are also critical.
Material Compatibility Testing ensures that cleaning solutions are compatible with non-destructive testing (NDT) procedures and will not adversely affect rubber, sealants, or other sensitive materials.
Conclusion
Proper cleaning of aerospace and aviation parts is essential for ensuring aircraft safety, performance, and compliance with stringent industry standards. By understanding the common contaminants, selecting appropriate cleaning methods, and adhering to required cleanliness testing and certifications, aviation professionals can maintain the reliability and efficiency of their components.
Whether dealing with OEM or MRO components, JAYCO Chemical Solutions provides a range of specialized cleaning solutions to meet the needs of the aerospace industry certifications, ensuring high performance and safety standards are consistently met.