Citric Passivation vs Nitric Passivation: Key Differences
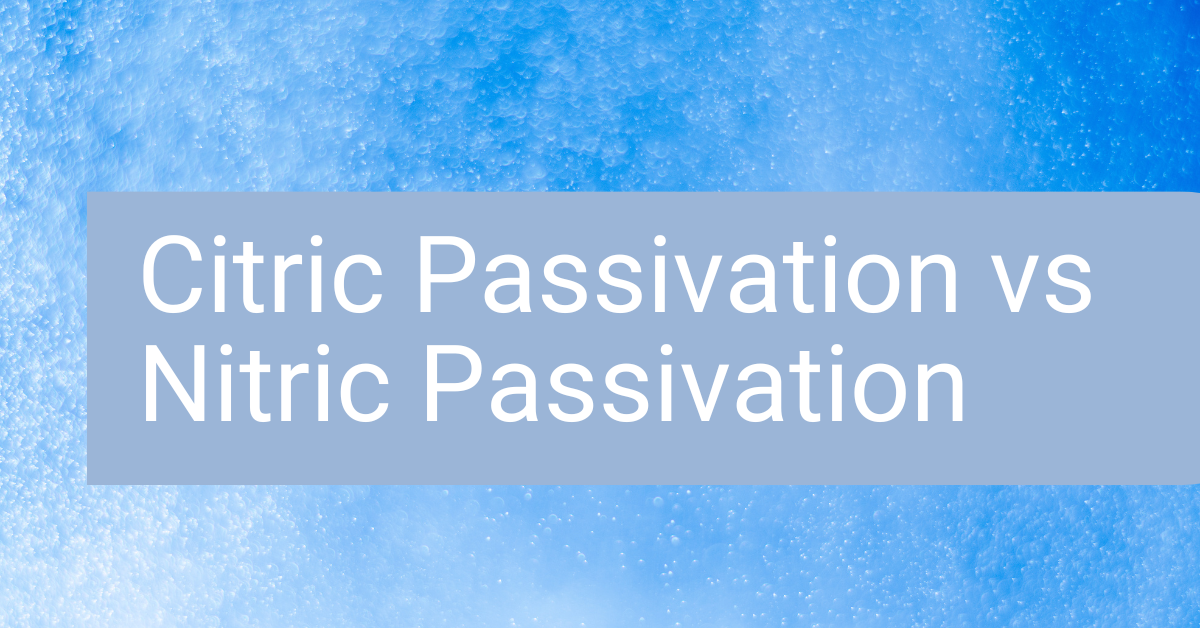
Stainless Steel’s Natural Protection
For industrial and commercial applications requiring long life, high corrosion resistance, and superb mechanical performance, stainless steel alloys are the materials of choice. These alloys derive their name from their high chromium and low carbon contents, making them very resistant to “staining” (thus, stainless) or corroding even in aggressive environments.
In professional uses, stainless steels are most often supplied in austenitic alloy groups referred to as the 200 and 300 series. The 200 and 300 series are chromium-nickel alloys, non-magnetic, and often produced with advanced nitrogen-addition processes that further enhance their corrosion resistance. Most notably, alloy Types 304 and 316 make up the vast majority of stainless steel equipment, vessels, instruments, utensils, structures, and hardware used in hygienic and otherwise harsh conditions.
The chromium content within stainless steel materials naturally reacts with airborne oxygen in a very curious way. Chemically-speaking, chromium is a reducing agent which reacts with oxygen as an oxidizing agent in ambient conditions, together producing chromium oxide molecules on the surface of the chromium-containing body. (Reaction formula 4Cr + 3O2 → 2Cr2O3).
This chromium oxide film slowly develops without any other catalyst, and once complete, provides a fully unreactive or “passive” layer protecting the stainless steel material underneath. At only a few molecules in thickness and completely invisible to the naked eye, this passive layer inhibits contact between the stainless steel surface and foreign objects – especially those that tend to lead to corrosion, such as oxygen and moisture.
Chemical Passivation
While it’s a wonder of natural chemistry in action, this chromium oxide passive layer is not free from practical concerns. The passivation process takes some time to occur naturally, and is nearly impossible to inspect for assurance that it has evenly developed at all. Also, normal fabrication processes as well as everyday wear-and-tear will destroy this passive layer anywhere that high physical force, heat, electrical current, certain chemical reactions, or abrasion may occur on a stainless steel body. For these reasons, intentional processes have been developed to spur generation of the passive layer on-demand, which we refer to as Chemical Passivation.
Industrial chemical passivation is performed in several steps:
- Alkaline Wash – a thorough washing process is performed on the stainless steel materials to be passivated, which strips away all contaminants on the materials whose presence would interrupt the even formation of a new passive layer. Washing removes all oil, grease, coolants, polishing compounds, and other foreign matter on the part, otherwise corrosion may continue to develop where these soils remain.
- Rinse – after washing, all residual trace chemicals are removed by rinsing the part in clean, neutral water. Water sources must be selected intentionally so as not to reintroduce any contaminants to the cleaned part.
- Acid Bath Passivation – the stainless steel part is now introduced into an acid bath where passivation will occur. The acid bath is made up of one or more chemicals (discussed below), diluted to a specific concentration, and often heated as well. The part is submerged in the bath for a set amount of time as the passivation process takes place.
- Rinse – upon completion of the passivation bath, the part is removed and rinsed again. As with the initial rinse, this rinse must thoroughly remove all trace residues, and may include a separate chemical treatment step that aids in rinsing and neutralization. Water must be of high quality and have no more than 200 ppm maximum total solids.
- Dry – after final rinsing, the part is dried off by recirculated hot air with optional vacuum dry, completing the passivation process.
Upon completion of the passivation process, it is relatively certain that the stainless materials have formed an even, continuous chromium oxide passive layer across all surfaces. Ensuring that the passive layer has formed can be difficult. Testing procedures do exist, however most passivation tests measure the presence of free iron on a stainless steel surface, not the passive layer itself. Testing for free iron is rooted in the assumption that if excessive iron is present on an SS surface, that the passive layer must be compromised and in need of replacement. Since in most cases we cannot practically inspect that the passive layer itself has formed, users typically rely on established procedures backed by standardized lab testing which strictly specifies the chemical type, chemical concentrations, temperatures, and amount of time used in the chemical passivation process.
Though we just stated that chemical passivation processes are strictly controlled and standardized, there is one large variable that is left to user discretion, and in fact has become a hotly debated topic over the last decade – that is, what specific chemical to use for the best overall results. Let’s dive into that debate next!
A Passive-Aggressive Debate in Chemistry – Nitric vs Citric Acid
What are we looking for in a passivation chemical? Three things:
- Works fast – we want to limit reaction time and get the parts through production
- Must be effective – we want the highest reasonable likelihood that the new passive layer is formed
- Must be manageable – industrial chemicals tend to have risks associated with their use, so we want a solution that does not cause undue risks or hazards
As so many things go, the market provides multiple options offering a different mix of benefits across the above listed items. The two most common options available today are Nitric Acid and Citric Acid, each with their own distinct upsides and downsides.
Nitric Acid
Historically, Nitric Acid has been the most common agent utilized in chemical passivation. Nitric acid is aggressive, attacking contaminants and trace elements such as free iron quickly, which speeds up the overall passivation process described above.
For nitric acid to work effectively however, high temperatures and high concentrations are necessary – on the order of up to 160*F and up to 55% concentration by volume. This makes nitric acid passivation extremely aggressive, presenting potential risk factors to human operators, the equipment, the environment and sensitive parts being passivated.
Citric Acid
Recent advancements in chemistry and material science have brought forth a modern, sustainable alternative for chemical passivation: Citric Acid. Citric is much safer, can be ran at lower temperatures (from ambient to 120*F), diluted to much lower concentrations (4% to 10% by volume), and for less time. Though synthetically manufactured for industrial uses, citric acid is naturally-occurring and generally considered “edible” and “food-grade”, presenting a much less hazardous profile than nitric acid. Citric acid is biodegradable, and much less impactful to waste water as well.
JAYCO’s proprietary formulations of Citric Acid geared towards stainless steel passivation deliver additional benefits for our customers.
- Passive layers equal or greater to nitric acid
- Inhibited microbial growth without the use of added biocides,
- Improved ultrasonics cavitation, as well as very high rinsability (reduced DI/RO water consumption).
- Works very well with automated process controls, which includes monitoring and dosing systems.
Conclusions
We’re left with a simple comparison to make: nitric passivation vs citric passivation, or something else? The decision lies in each use case, for the most part.
Nitric Acid is a more aggressive solution requiring more effort, energy, and risk, however may be the required solution in certain applications that need the microbial destruction, and organic soils removal (such as in medical device and biotech industries).
Short of these few niche cases, Citric Acid is the new, modern solution for stainless steel passivation. Being safer, easier to handle, more environmentally-friendly, and overall less demanding to use, Citric Acid wins out on practically every front. Further, by using special formulations targeting your application’s specific requirements, JAYCO’s Citric Acid Passivation chemistries can accomplish passivation levels comparable to nitric blends in a much safer, biocide-free, employee-conscious way.
Are there other options available? Yes! Various other acids such as phosphoric acid and dichromate are available, however such options are notably more aggressive and hazardous than citric or nitric acids. On the other end of the spectrum, newly emergent, organic, and bio-safe formulations are well into development, offering users a new generation of technical, reliable, and environmentally-conscious solutions. JAYCO Chemical Solutions is at the forefront of such advanced formulations in chemical passivation technologies, and we’re ready to demonstrate our novel solutions on your next passivation project.
JAYCO Chemical Solutions is North America’s single-source provider of engineered cleaning solutions. From process analysis and application engineering to delivery and support, JAYCO improves operations for precision metal, medical, optical, UHV, space/aerospace and general manufacturing customers. For more information on JAYCO Chemical Solutions, our products and our markets, please call us at (814) 593-0022, or email us at info@jaycochem.com.