Tackling Today’s Medical Device Parts Cleaning & Passivation Challenges with Modern Detergents
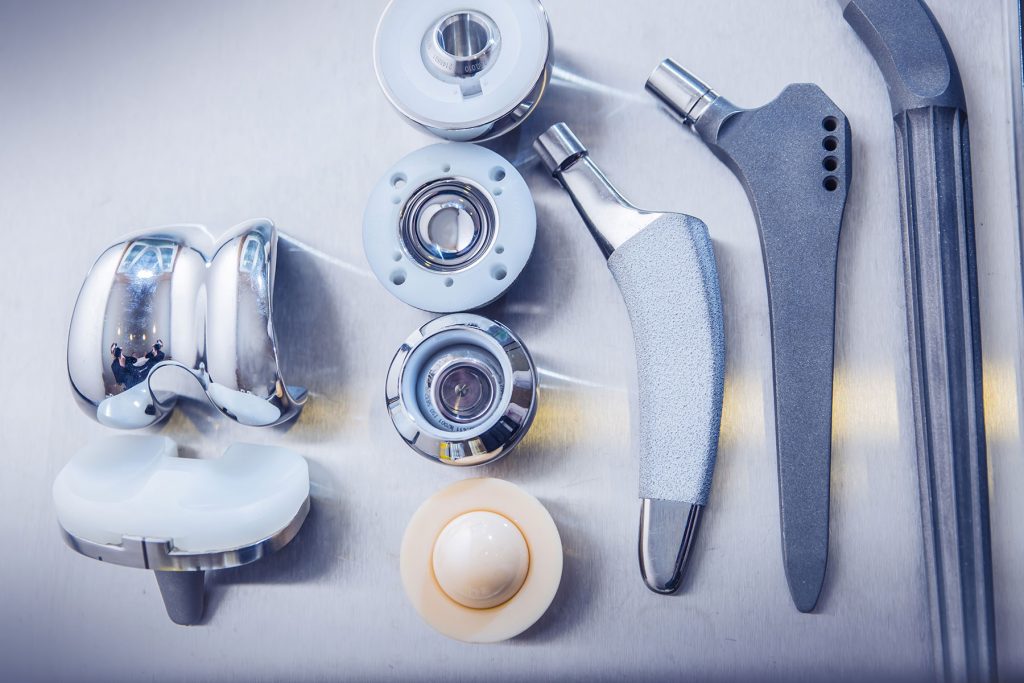
Medical device and implant makers are feeling the squeeze when it comes to parts cleaning. OEM specs, global standards, and environmental rules keep tightening—while geometries get smaller and materials more diverse. If your washer, passivation tank, or chemistry recipe hasn’t changed in a few years, you may already be behind.
Below are the six emerging pain points we hear from shops regularly—and the chemistry strategies that keep process engineers and quality managers happy.
Achieving Sub-Micron Particle Count
What changed
- ISO 19227 sets quantitative particulate count and TOC limits for orthopedic implants, down to 0.5 µm and 0.5 mg/implant. ITEH Standards
Modern chemistry playbook
- High cavitating detergents – lower surface tension so ultrasonic cleaning can better remove particulate out of blind holes. Consider JC 400M for medical ultrasonic cleaning.
- Low foaming surfactants – maintain cavitation intensity and drain fast.
- Rinsability metric – target final rinse conductivity < 1 µS/cm and water break free on the surface.
Escaping Nitric-Acid Headaches
What changed
- Nitric passivation generates NOx fumes and requires 25 – 50 % acid—raising EHS and permit costs. Technical Reports
- ASTM F86 remains the corrosion-resistance yardstick. ASTM International
Modern chemistry playbook
- Buffered citric acid blends – strip free iron without NOx and rinse off in two DI stages. Consider JC CitraPass 5220M.
- Mixed acid systems – trace nitric for speed, citric for operator safety.
- Neutralization checklist – verify wastewater pH stays 6 – 9 without over-titration.
Rinsability tip – Well buffered citric leaves near-zero ionic residue and won’t flash rust fixtures when rinse flow exceeds 1.5 gpm / ft² basket area.
Precision Cleaning Additive Manufactured Lattice Structures
What changed
- ASTM F3335-20 defines a test method for proving complete removal of powder-bed-fusion residues from medical devices. ASTM International
- AM Ti and CoCr lattices under 300 µm trap sintered powder and recast oxide. SpringerLink
Modern chemistry playbook
- Ultra-low surface tension detergents (< 22 dyn/cm) seep into capillaries.
- Peroxide boosters oxidize stubborn recast without attacking Ti substrate.
- Vacuum-assisted pulsing in the ultrasonic tank mechanically assists removal of loose trapped powder. Consider JC 401SC for vacuum-assisted rotary basket washers.
Rinsability tip – Two to three stage DI rinses with flow agitation plus TOC trending ensure pores flush clean.
One Line, Four Alloys: Managing Cross-Material Risk
What changed
- Implants now mix 17-4 stainless steel, Ti-6Al-4V, CoCr, nitinol, and PEEK—each with different pH and oxidizer tolerances. SpringerLink
Modern chemistry playbook
- Flexible detergents – choose an alkaline or neutral cleaner that is compatible with all materials. Consider JC 400M cleaner.
- Dedicated fixtures or pads – prevent galvanic cross-contamination.
Rinsability tip – Use chemistries that rinse neutral (pH 6 – 8) to avoid nickel leach from nitinol or hydrogen embrittlement in high-strength steels.
Solvent & PFAS Phase-Outs
What changed
- EPA designated PFOA & PFOS as CERCLA hazardous substances in April 2024. US EPA
- The EU is advancing broad PFAS restrictions under REACH (2024 draft). European Chemicals Agency
Modern chemistry playbook
- Aqueous high alkaline washes tackle oils and coolants.
- Hot-air knives + vacuum assisted drying offset the absence of fast evaporating solvents.
Data Integrity & Audit-Ready Records
What changed
- MDSAP audit model requires batch records that prove traceability and cleaning effectiveness. U.S. Food and Drug Administration
- 21 CFR Part 11 demands secure, tamper-evident electronic records. Regulatory Compliance
Modern chemistry playbook
- Chemistries detectable by conductivity enable automated end-point control.
- PLC-linked dosing pumps log adds directly to your historian.
- Cloud archives preserve five-year traceability—no paper binders.
Turning Compliance Pressure into Competitive Advantage
Cleanliness specs, solvent bans, and digital audits aren’t slowing down. Shops that treat cleaning and passivation chemistry as a strategic lever—not a commodity—pass audits faster, cut scrap, and move new implants to market sooner.
Not sure if your current process is future-proof? Run a no-cost cleaning test with the Jayco Chemical Solutions applications lab. The data will show exactly where you stand—and where modern chemistry can take you.