Isotropic Superfinishing – How To Achieve A Precision Finish Thru A Chemically Accelerated Surface Finishing Process

Quick Take
Isotropic superfinishing is a chemically accelerated finishing process commonly used in aerospace, medical, defense, and automotive component manufacturing where surface finish is critical for proper operation and reliability. Superfinishing can typically achieve Ra values below 0.1 µm (4 µin), and in an optimized process can be reduced to as low as 0.025 µm (1 µin) which is significantly better than conventional finishing methods.
This cutting-edge process not only makes parts smoother, but also stronger and more durable. Jayco offers two modern solutions for isotropic superfinishing chemistries, the combination of JC 840L / JC 680B or JC 813L / JC 670B. Both offer outstanding surface finish, reduced cycle times, and are environmentally friendly.
What is Isotropic Superfinishing (aka Chemically Accelerated Surface Finishing)?
Isotropic superfinishing is a high-tech process that makes the surface of parts incredibly smooth and uniform. The term “isotropic” means that the physical properties are the same in all directions, which in this context means the surface is even and free from any rough spots, peaks, or valleys. Imagine polishing a rough stone until it’s completely smooth and shiny – that’s essentially what isotropic superfinishing does, but on a microscopic level.
During traditional manufacturing processes like machining, molding, or casting, parts can end up with surface imperfections like tiny peaks, grinding marks, or burrs. Isotropic superfinishing removes these imperfections, resulting in a surface that is almost perfect. This smooth finish can only be seen under a microscope, showing just how precise the process is.

Benefits of the Isotropic Finishing Process
The benefits of isotropic superfinishing are numerous and impressive:
Surface Quality
Creates an incredibly smooth surface, reducing roughness to a minimum. This is especially important for parts that need to fit together precisely, like gears in a car engine.
Fatigue Resistance
By smoothing out the surface, it helps parts resist fatigue better. This means they can handle more stress and last longer without breaking down. It’s like having a well-oiled machine that just keeps running smoothly.
Friction Reduction
A smoother surface means less friction. This is crucial for parts that move against each other, like in engines or machinery. Less friction means less wear and tear, leading to longer-lasting parts and more efficient machines.
Cleanliness and Durability
Makes surfaces not only smooth but also clean and durable. This is particularly important in industries like medical and aerospace, where the slightest imperfection can lead to big problems. For instance, smoother surfaces on medical implants reduce the risk of infection and improve compatibility with the human body.
Environmental Benefits
The process is often more environmentally friendly due to reduced chemical usage and waste production. This makes it a more sustainable choice for manufacturers.
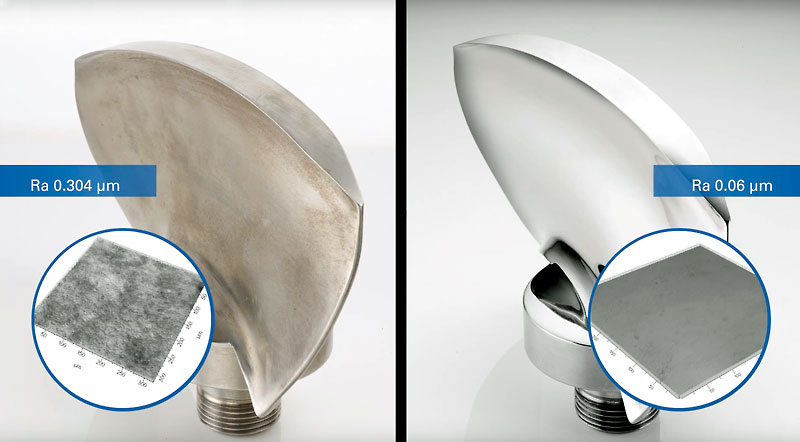
The Isotropic Superfinishing Process: Steps and Chemicals in the Vibratory Finishing Method
Isotropic superfinishing, particularly when using the vibratory bowl method, involves several key steps to ensure a uniformly smooth and polished surface. This method is highly effective due to the combination of mechanical action and chemical assistance. Here’s a detailed look at the process:
1. Preparation of Components
Before the actual finishing process begins, components are thoroughly cleaned to remove any contaminants such as oils, dirt, or residues that might interfere with the finishing process. This ensures that the chemicals used can interact directly with the metal surface.
2. Loading the Vibratory Bowl
The cleaned components are placed into a vibratory bowl along with abrasive media. The media typically consists of small, abrasive pellets made from ceramic, plastic, or other materials suitable for the specific type of metal being finished.
3. Adding Accelerating Chemicals
Special chemicals are added to the vibratory bowl to enhance the finishing process. These chemicals play a crucial role by reacting with the metal to form a conversion coating on the surface. This coating is softer and more easily removed, which allows the abrasive media to smooth the metal surface effectively. Use Jayco JC 840L or JC 813L modern acidic formulations for the refinement stage.
4. Refinement Stage
Once the components, media, and chemicals are in the bowl, the machine is activated. The bowl vibrates at high frequencies, causing the media and parts to rub against each other. This mechanical action, combined with the chemical reaction, removes the softer conversion layer, exposing fresh metal underneath.
As the conversion coating is abraded away, new metal is exposed to the chemicals, forming a new layer. This cycle of coating and abrasion continues, gradually reducing the surface roughness and smoothing out peaks and valleys on the metal surface yielding a uniformly smooth and isotropic surface.
5. Burnishing Stage
Once the desired surface finish is achieved, the process transitions to the burnishing step. The chemical compounds are replaced with alkaline cleaning solutions to remove any residual conversion coating. This step also helps to visually brighten the surface, giving it a polished appearance. Use Jayco JC 680B or JC 670B modern alkaline formulations for the burnishing stage.
6. Final Cleaning and Inspection
After the burnishing step, the components are thoroughly cleaned to remove any remaining chemicals or abrasive media. They are then inspected to ensure they meet the required specifications and quality standards. Any remaining roughness or defects are addressed before the parts are deemed finished.
7. Drying and Packaging
Finally, the finished components are dried to prevent any corrosion or damage. They are then packaged appropriately for storage or shipment.
Compared to traditional methods, isotropic superfinishing is faster and produces a higher quality finish. Traditional methods might leave behind some imperfections, but isotropic superfinishing ensures a uniformly smooth surface with no marks or lines.
Explore how Jayco Chemistry Solutions can help your finishing operations.