Precision Cleaning Solution Buying: How Much Do I Need In Inventory?
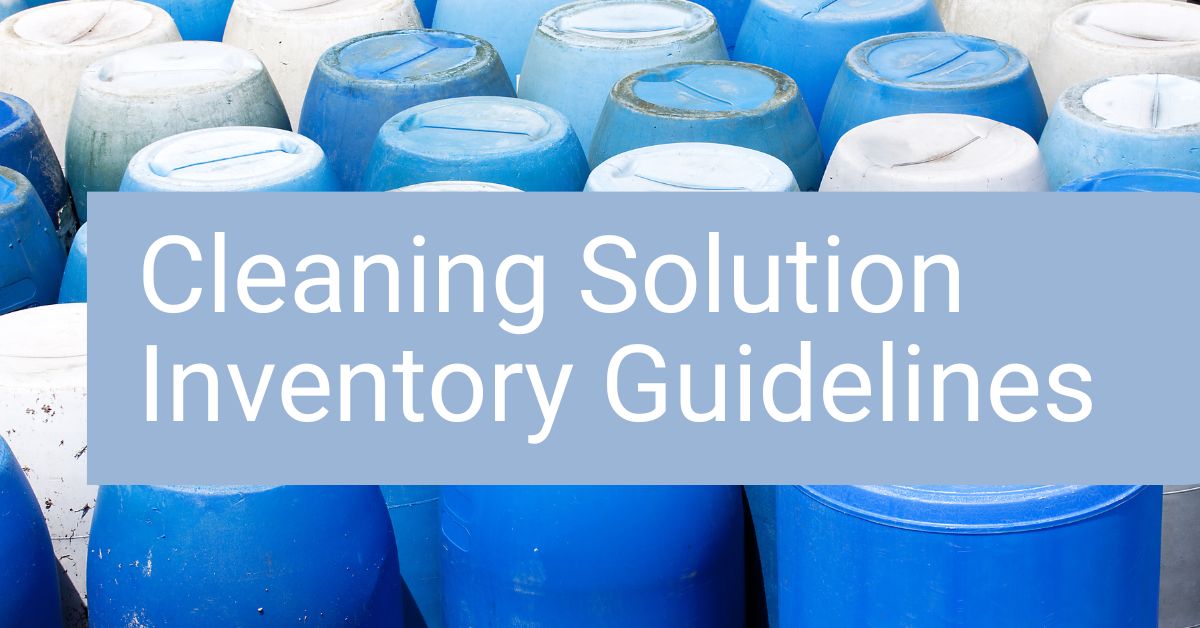
Precision Cleaning Applications
Manufacturing industrial goods can be a dirty business, and an entire industry segment known as precision cleaning has evolved over the last few decades to help clean it up. Polishing, deburring, degreasing, surface treating, burnishing, rust inhibiting and even microbial sterilization are all types of precision cleaning and mass finishing processes found in industrial manufacturing.
Both automated cleaning equipment and manual finishing toolsets are used to perform precision cleaning work. The secret ingredient is found within the specially formulated, engineered chemical solutions employed in these processes. These technical chemistries are custom designed to unlock and bolster superior performance in each mass finishing application. The solutions provide functional benefits resulting from targeted chemical reactions, molecular bond exploitation, residual material reinforcement and contaminate and soil destruction.
Since these chemicals are so valuable and necessary in manufacturing workflows, precision cleaning solution buying is a critical business topic. How do we secure reliable chemical supply? How much should we order? How much should we keep in inventory? How do we protect ourselves against future supply chain issues like we’ve seen recently?
These are very important questions. Here, we outline a method for calculating inventory levels of precision cleaning chemicals, as well as offer suggestions on how to further optimize chemical inventory expenditures into the future.
Determining Inventory Levels
Turning to industrial engineering principles, we can put together a surefire method for calculating inventory levels of most consumable goods. Applying these methods to mass finishing and cleaning chemicals works exactly the same way, though with an added step dealing with chemical concentration and dilution proportions. Follow these steps to arrive at minimum and maximum chemical Inventory volumes when buying precision cleaning solutions.
Step 1: Calculate Daily Consumption
Most businesses will consume chemicals in either a “batch” or “continuous” manner, and we can use simple formulas to estimate a daily consumption volume for either type.
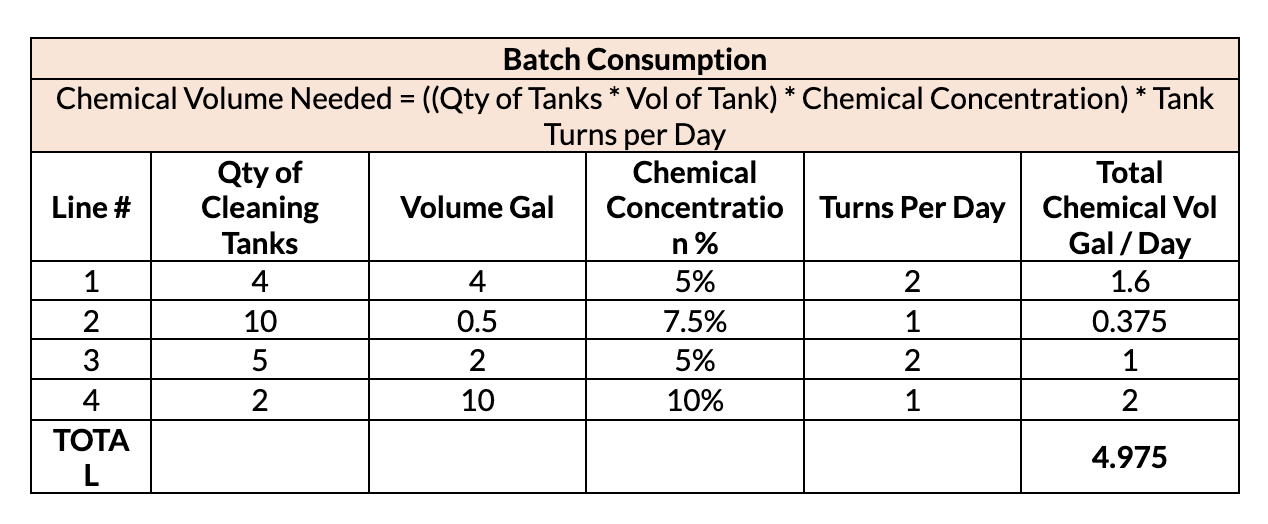
The above batch consumption example provides us with a total daily chemical load required to fill up all of the various sized tanks shown to their required concentrations, and to refill the tanks that are emptied and refilled (or “turned”) each day as well. The above example says we need 4.975 gallons of chemicals to fulfill one day’s worth of production. Note that in this simple example, we’re assuming that all tanks are filled with the same chemical to varying concentrations: Your operation will most likely have multiple chemicals, and you would perform this calculation for each unique chemical.
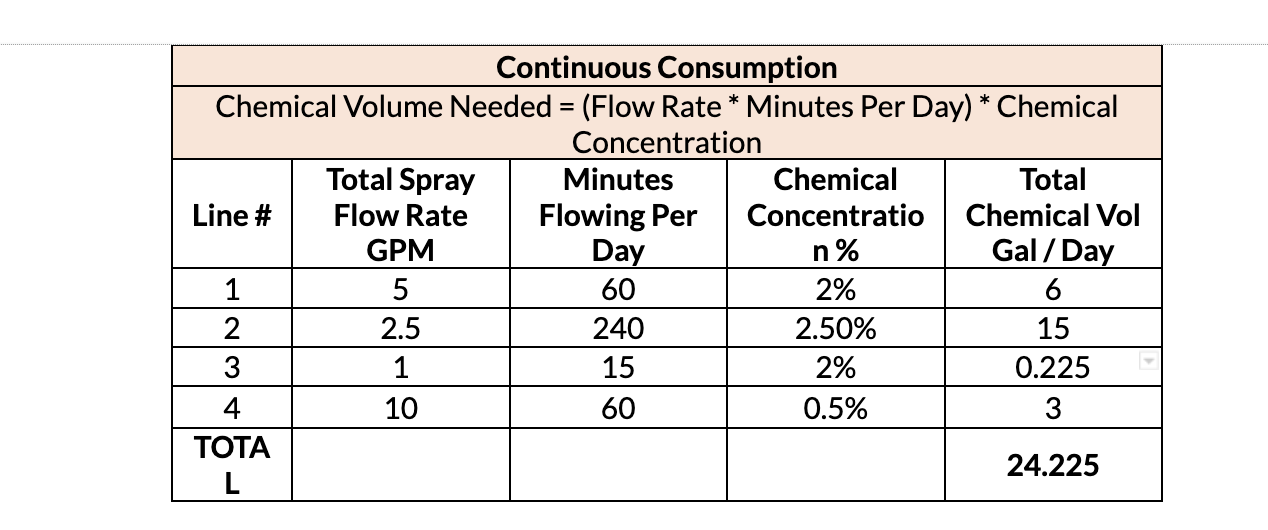
Our continuous consumption table above reflects processes such as spray and rinse equipment, which deliver a steady flow of chemical-containing solution over parts. We call this a “100 percent make-up” type system when all of the rinse water and chemicals delivered go directly to the drain without recirculation. (For recirculating systems where a common feed tank is filled and emptied periodically, you would use the above batch consumption type calculation instead.) Here again we assume that all lines are receiving the same chemical to reach one daily total.
Now that you have your totals, add them together. From the above, we have 4.975 gallons + 24.225 gallons = 29.2 gallons per day of the chemical in question.
Step 2: Calculate Order Period
Now multiple the daily chemical volume needed by your most common order period: Let’s say once a month, or every four weeks. Operating five days per week, that would be 4 weeks * 5 days/week = 20 days.
Step 3: Calculate Stockout Protection
If you place an inventory order every month, and if you only order the exact amount you need for that month, in effect you will receive your new order exactly when the previous order runs out. For most businesses, this approach is risky. What if the order is delayed, mis-delivered, out of stock or completely lost by the vendor? You want to have some additional stock on hand in all these cases, providing you a reasonable safety net. The last thing you want is to halt production while you wait for chemicals to arrive. The amount of additional days’ worth of inventory to have on hand (in addition to your normal consumption volume) is known as stockout protection.
There are several things to consider when deciding on how much stockout protection you need, such as:
- Alternative sourcing. The number of days it would take to order inventory from an alternative source, if your primary source is out of stock.
- Delivery range. The highest number of days that the supply chain takes to deliver an order.
- Local stop-gap supply. In the event that normal channels are not able to deliver your order, the number of days you’d need to find a local stop-gap supplier that you could physically pick up inventory from.
- Realization period. If you place your order and all responses from the vendor are normal, but the order ultimately doesn’t arrive, this measurement includes the number of days it would take your team to become aware of the issue and decide that a change of plans is necessary.
- Critical order fulfillment. If you generally take volume orders from clients that must be completed in lots, the number of days it takes to run that production can be used as the amount of stockout protection days desired. For example, if you have accepted a work order that will take 60 days of production to complete, it may be wise to put 60 days of chemical inventory in stock, so that chemical delivery does not jeopardize fulfilling the client’s order.
- Comfort level. Assessment of your personal comfort level in terms of additional days of stock to have at any given time.
Most likely, the amount of stockout protection days your business will desire will be a combination of all of the above (and other) factors. For this example, let’s use these parameters: You place an order for 20 business days, which usually takes one week to arrive, but if on the second week you notice that it has not arrived for any reason, you want to have up to a third week of inventory to acquire alternative supply. So, you would need three weeks’ or 15 business days’ worth of stockout protection.
Step 4: Calculate Inventory Volume Required
Now you can calculate your inventory requirements for the specific chemical.
From the above, you have established that you want no less than 15 business days’ worth of stockout protection on hand at any given time. Call this your minimum inventory level.
Following these example calculations, you also concluded that you would order on 20-business-day frequencies (or one order per month), which if delivered the same day as ordered, would see you having the combined 20 days of operation plus the 15 days of stockout protection, totalling 35 days’ worth of inventory. Call this your maximum inventory level.
You can now calculate these volumes for precision cleaning solution buying:
Minimum inventory level (15 days) * Daily consumption (29.2 gallons / day) = Maximum inventory volume (438 Gallons)
Maximum inventory level (35 Days) * Daily consumption (29.2 gallons / day) = Maximum inventory volume (1,022 Gallons)
Using these calculations, you arrive at needing a minimum inventory volume of 438 gallons, and a maximum inventory volume of 1,022 gallons of the chemical in stock at any given time.
Optimizing Inventory Management
Figuring out the above starting volume is only half of the inventory management battle. Over time, managers will want to refine and optimize their inventory levels when precision cleaning solution buying. They want to be properly prepared for unforeseen inventory issues without sinking unnecessary money into holding too much stock. Let’s discuss a few strategies for optimization next.
Referring to the calculations above, you might think that while the minimum volume of 438 gallons makes sense for stockout protection, the max volume of 1,022 seems quite a bit higher; potentially even too high. This maximum should be interpreted as the max amount that would be received with the very first order, and at any time that a full month is ordered while also having a full stockout volume in stock. The underlying decision that makes this max volume so high is found in step 2 above, where it was decided to place orders once a month. Ordering in smaller batches more frequently, such as every two weeks, can reduce this maximum inventory number, but will add more administrative work, shipping charges and handling effort.
Businesses will typically start tuning up their inventory volumes by reducing their maximum volume over time, as they become more comfortable with the reliability of their vendors, as well as stability of their consumption rates. Likewise, businesses will next press on their minimum inventory volume, reducing their stockout protection volume for the same reasons.
Once the minimum and maximum values are massaged over time, additional inventory optimization steps can be taken to reach the right inventory volumes, smooth out inventory spending, cut down on wasting inventory space and properly insulate against market and customer changes. Examples of steps to take over time include:
- Tracking and forecasting inventory levels using purchasing software.
- Ordering mass finishing chemicals in different volume containers, where larger containers such as drums and totes typically have a lower volume cost than smaller containers. (This approach also cuts down on wasted space and packaging.)
- Partnering with your chemical suppliers to maintain minimum volumes at their facility for you, using their facility as “off site” inventory space in order to free up storage areas in your facility. Minimum in-stock volumes typically can be negotiated as part of a master service or ongoing purchasing agreement.
- Automating chemical delivery using automatic dosing pumps, concentration sensors and other quality instruments. These tools reduce human error, waste and overuse of chemicals. This allows consumption rates to be improved and can help reduce the need for excess inventory.
- Evaluating your manufacturing and cleaning equipment for further efficiency gains and chemical use reduction. In many cases, replacing aging equipment with more efficient or higher volume models can drastically impact chemical consumption, as can reviewing existing equipment usage to make sure they’re being operated in an ideal manner.
Questions on Precision Cleaning Solution Buying?
JAYCO Chemical Solutions is North America’s single-source provider of engineered cleaning solutions. From process analysis and application engineering to delivery and support, JAYCO improves operations for precision metal, medical, optical, UHV, space/aerospace and general manufacturing customers. For more information on JAYCO Chemical Solutions, our products and our markets, please call us at (814) 593-0022, or email us at info@jaycochem.com.